General Operating Procedures for ThermRods
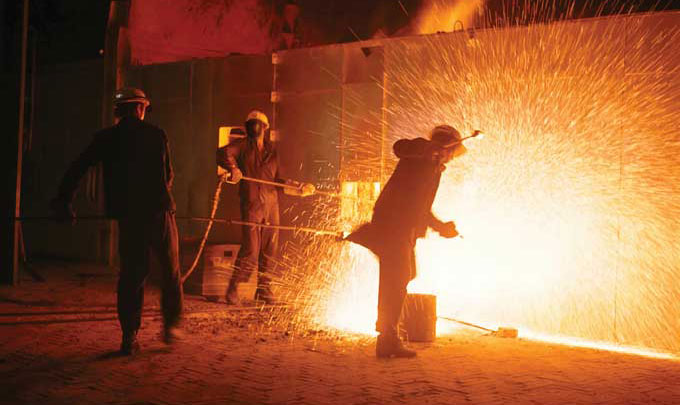
“Personal safety depends on sincere safety-mindedness and good judgment on the part of each individual, not on occasional intervals, but continuously as an integral part of daily activity.”
The best insurance against accidents and injuries may be summed up in five short sentences.
- Know your job and the pertinent safety rules.
- Be aware of hazards in the work area.
- Keep your mind on the job.
- Use common sense.
- If you can’t do it safely, don’t do it.
Improper use of ThermRods can result in personal injury or death. It is essential all exothermic cutting tools be used in accordance with these instructions in conjunction with site specific safety operating procedures. Therefore, study information carefully to insure you understand all instructions completely prior to use of exothermic cutting tools.
ThermRods, Burning Bars and Lance Pipe (exothermic cutting) generate temperature in ranges exceeding 6,600°F to 8,000°F. When properly used, it is a highly effective tool.
ThermRods
- A ThermRod is a smaller diameter tube filled with wire that acts as the catalyst to sustain burning.
- ThermRods are available in 2′, 3′ and 4′ sizes, although any length is possible.
- ThermRods are produced in two (2) standard outside diameter sizes, 1/4 (.250) and 3/8 (.375) inches.
- The 3/8″ ThermRod has a quick connect (expanded) end. QC ThermRods can be coupled together to allow operators to move as far away as possible from the work area. QC ThermRods virtually eliminate waste.
- The ThermRod Handle can be used for both sizes of ThermRods. Only the collet needs to be replaced.
GENERAL PRECAUTIONS
- Using oxygen at high flow rates requires adequate evaporators to handle the volume. Oxygen at high flow rates produces a refrigeration effect. It is essential that adequate evaporation is utilized. Check oxygen system on a regular basis and ensure there is no freezing in the system after the evaporator. If freezing occurs shutdown the system immediately, determine and solve the problem before restarting the system.
- The ThermRod system should be used only by workers fully trained and qualified in every aspect of burning.
- Although use of the ThermRod system is a one (1) person job, it is recommended a second (2nd) person be in the general work area should a problem arise.
- All workers in the area of the burning must wear appropriate personal protective equipment (PPE), which will include safety shield and welders leathers and welders gloves, as well as hardhat, safety shoes and safety glasses. Depending on the conditions, additional PPE may be required.
- Ensure all fire protection procedures are in place. It is recommended a fire watch procedure is used.
WORK SITE PREPARATION
- Prior to using ThermRod(s), thoroughly inspect the work site for hazards and potential hazards (i.e., oil & grease, physical restrictions, flammable materials, confined spaces, utilities, tripping hazards, etc.). Identify and remove these hazards where possible. Plan work to avoid hazards which cannot be removed.
- Obtain and implement the required burning permit(s).
- Obtain and implement the required fire procedure(s).
- Identify at least one (1) evacuation route.
- Be sure there is proper ventilation for smoke and gases which will be created during the burning process. A respirator (and/or supplied air hood if required) should be worn by all workers involved in the burning or exposed to smoke and gases created by burning.
- Depending on the material being burned, scrubbing of smoke may be required.
- Review MSDS sheets of the Burning Bars & Lance Pipe. Check the MSDS of material being burned for respiratory precautions prior to the start of work.
PERSONAL PROTECTIVE EQUIPMENT (PPE)
The equipment required for personal protection can vary based on work site conditions and the material being burned. Each site should be thoroughly evaluated for identification of all appropriate protective equipment.
- All workers involved in burning must wear welder’s leather clothing, welding gloves and face protection/shield, safety glasses and a respirator.
- A protective shield and/or scaffold shield may be required to guard against splash back of materials when burning a surface which prohibits the slag/molten materials from flowing easily away from the operator.
GENERAL SAFETY REGARDING THE USE OF OXYGEN
- Be aware of possible clearance problems and site restrictions.
- Ensure all oxygen sources being utilized are individually regulated and set at the desired operating pressure, which is recommended not to exceed 80 psi. for ThermRod(s).
- Use high pressure oxygen hose with a minimum pressure rating of 200 psi.
- All equipment (hoses, handles, valves & fittings, etc.) used in the burning process must be “approved and cleaned” for oxygen service. Degreasing must be carried out by qualified personnel.
- Oxygen is extremely reactive with combustibles, especially hydrocarbons like oil/grease/paint. Keep clothing and all burning equipment free of hydrocarbon materials.
- Keep bare skin away from oxygen.
- No smoking near oxygen or in work area where burning is occurring.
- To prevent damage and/or a sudden release of oxygen, do not kink hoses for any reason.
- Wear gloves when operating the burning bar system. Be aware of brass slivers from threads.
- Prior to beginning work ensure only authorized personnel are in work area and safely cordon the work area as required.
At the conclusion of lancing or burning, always turn off oxygen at source, disconnect oxygen hoses and equipment and store in approved storage area.
PREWORK INSPECTION
- Check area to ensure there is free access and no tripping hazards.
- Check all personal protective equipment to ensure it is in good condition.
- Ensure hoses are under/over stairways and walkways providing adequate clearance.
- Ensure Burning Bar ends are free from dirt and/or other obstructions.
- Check all valves to ensure they are free from dirt, oil and grease and are in good working order.
- Inspect the Burning Bar handle. Ensure valve on Burning Bar/Lance Pipe holder is in closed position. Do not use the Hot Rod handle if assembly appears to be damaged or worn.
- Ensure all hose, ThermRod handles and ThermRod(s) are connected securely with no leaks by trained operating personnel.
- Do not modify outlet pipes in any way. All changes to outlet, supply valves, etc. must be made by authorized and oxygen trained pipefitters.
- Refer to the Manufacturers’ Burning Bar and Lance Pipe Holder operating and maintenance procedure(s) for the handle being utilized.
- All hoses, fittings and handle connections must be tested for leaks prior to use. This is completed by pressurizing the oxygen system with the holder’s control valve in the fully closed position and checking each connection with Leaktec.
PRESTART / OPERATING
- Ensure handle/grip on ThermRod handle is in a closed position.
- Open oxygen supply.
- Check pressure gauge to ensure proper pressure setting. Insert ThermRod connection into holder. Open control valve on holder and with bare hand ensure there are no leaks at point Burning Bar/Lance Pipe enters handle.
- System is now ready to use.
- To ignite ThermRod(s) it is recommended a strike plate is utilized.
Turn on oxygen by triggering handle. Strike the ThermRod against the “DC-electric” striker plate until ThermRod ignites. Begin burn/cutting.
- ThermRod(s) consume relatively quickly. For example a 3/8 inch ThermRod, 2 feet long, consumes in 65 seconds.
- Do not burn the ThermRod shorter that 2 inches from the handle. This distance may vary depending on the holder being used and, in the case of a burning bar, the position of the crimping on the bar.
- When turning off the ThermRod ensure that the control valve/ handle grip on Holder is in the fully closed position.
- When a new bar is required the following steps must be taken:
The operator must shut off Burning Bar handle control valve to the fully closed position.
With heat resistant gloves, the operator is to disconnect the used bar (as per manufacturers handle/holder instructions).
Inspect the new bar and ensure there are no cracks; that it has not been contaminated; and that there are no plugged ends. If damage exists, discard.
Slip the new bar into the holder and secure.
Light the new burning bar as per instructions included herein.
SAFE USE OF THERMROD(S)
- Never point Burning Bars and/or Lance Pipe at anything you do not intend to burn.
- Keep oxygen hose away from molten metal, potential splashback areas and existing hazards.
- Direct bar so all workers and equipment are behind the ThermRod.
- Ensure oxygen flow and material splashback is away from workers. If this cannot be accomplished, construct shields for protection of workers.
- Should the burning bar be extinguished for any reason, shut off oxygen immediately, and remove burning bar from work area being burned to allow cooling. Inspect burning bar and determine why bar extinguished.
- It is recommended Burning Bar be replaced rather than reused.
STANDARD OPERATING PRESSURE FOR THERMROD(S)
1/4″ & 3/8″……….. 60 psi
The Safety Plan included herein, is generic and should be treated as a guide only in the preparation of a site specific plan. Site conditions such as confined spaces, fume collection, site specific hazards, oxygen supply systems, etc. need to be addressed and incorporated into the Job Specific Safety Procedures.
|